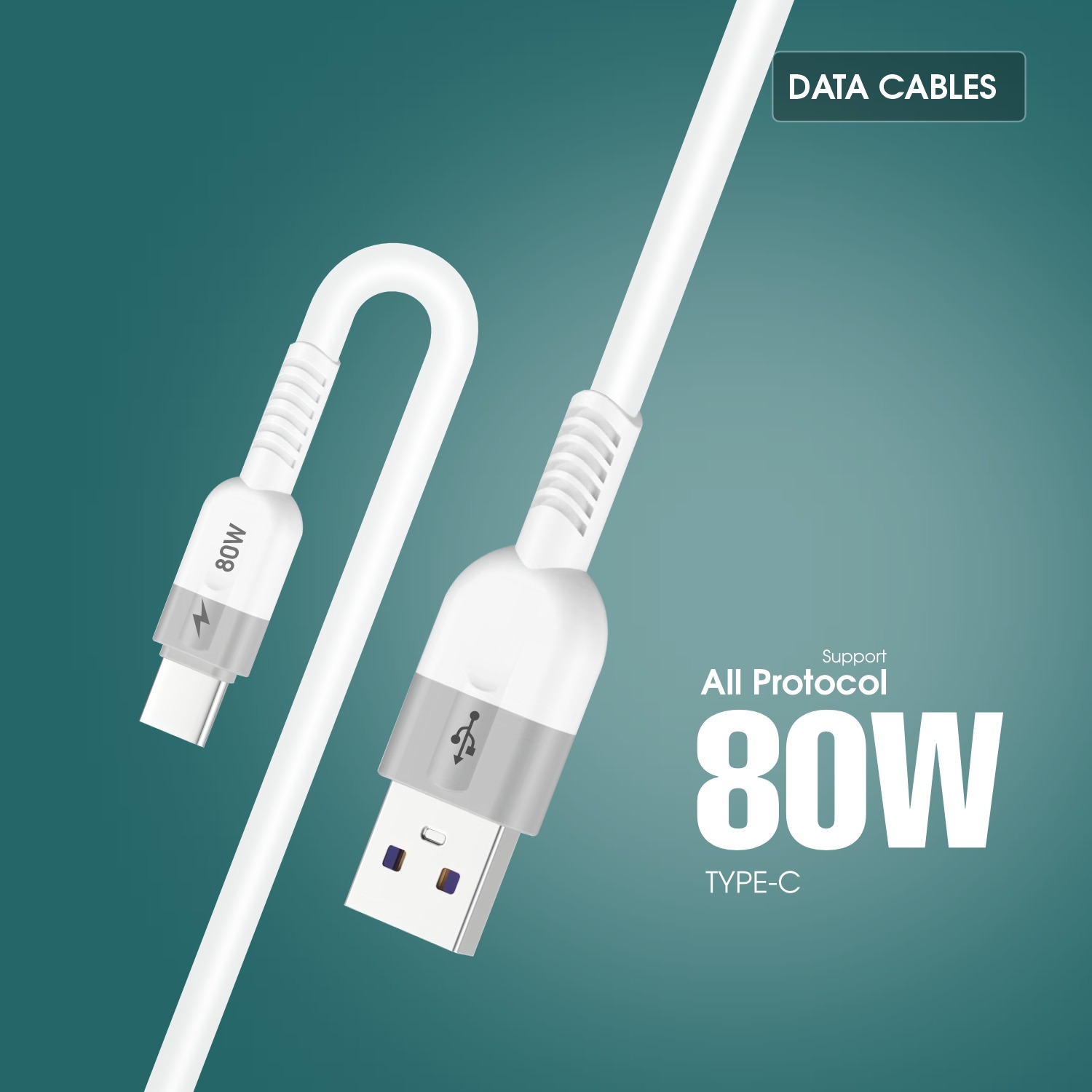
Data Cable
The manufacturing process of a data cable involves several key stages, from design and material selection to assembly and testing. Here’s an overview of the process:
1. Design and Development:
- Specifications: Define the technical specifications, including data transfer speed, length, connector type (e.g., USB, Lightning, Type-C), and durability.
- Prototyping: Create prototypes to test the design and functionality.
2. Material Sourcing:
- Conductors: Source high-quality copper wires for the conductors.
- Insulation and Sheathing: Obtain materials for insulation and sheathing, such as PVC, TPE, or braided nylon.
- Connectors: Source connectors, including metal parts, plastic housings, and gold or nickel plating for contacts.
3. Wire Drawing:
- Drawing: Draw copper rods through a series of dies to reduce their diameter to the desired thickness for the conductors.
- Annealing: Heat-treat the drawn wires to increase flexibility and reduce brittleness.
4. Stranding:
- Stranding: Twist multiple thin wires together to form a stranded conductor, which is more flexible and durable than a single solid wire.
5. Insulation:
- Extrusion: Use an extrusion machine to coat the stranded conductors with an insulating material, such as PVC or TPE.
- Color Coding: Apply color coding to the insulation to identify different wires (e.g., power, data, ground).
6. Cable Assembly:
- Twisting: Twist together the insulated wires to form the core of the data cable. For high-speed cables, additional shielding (e.g., foil or braided shield) may be applied to reduce electromagnetic interference.
- Sheathing: Extrude an outer sheath over the twisted wires to protect them from mechanical damage and environmental factors.
7. Connector Assembly:
- Crimping: Crimp the conductors onto the metal contacts of the connectors.
- Overmolding: Use an injection molding machine to apply a plastic overmold around the connector and the cable for additional strength and strain relief.
- Plating: Apply gold or nickel plating to the contacts to ensure good conductivity and resistance to corrosion.
8. Testing and Quality Control:
- Continuity Testing: Test each cable for electrical continuity to ensure there are no open circuits or shorts.
- Data Transfer Testing: Verify that the cable meets the specified data transfer speeds and standards.
- Durability Testing: Perform mechanical tests, such as bending, flexing, and tensile strength tests, to ensure the cable can withstand everyday use.
9. Certification:
- Compliance: Ensure the cables meet international safety and quality standards, such as CE, UL, and RoHS.
- Certification: Obtain necessary certifications from regulatory bodies.
10. Packaging:
- Design Packaging: Design and produce packaging materials, including boxes, manuals, and labels.
- Packaging Assembly: Package the cables securely for shipping, including bundling and labeling.