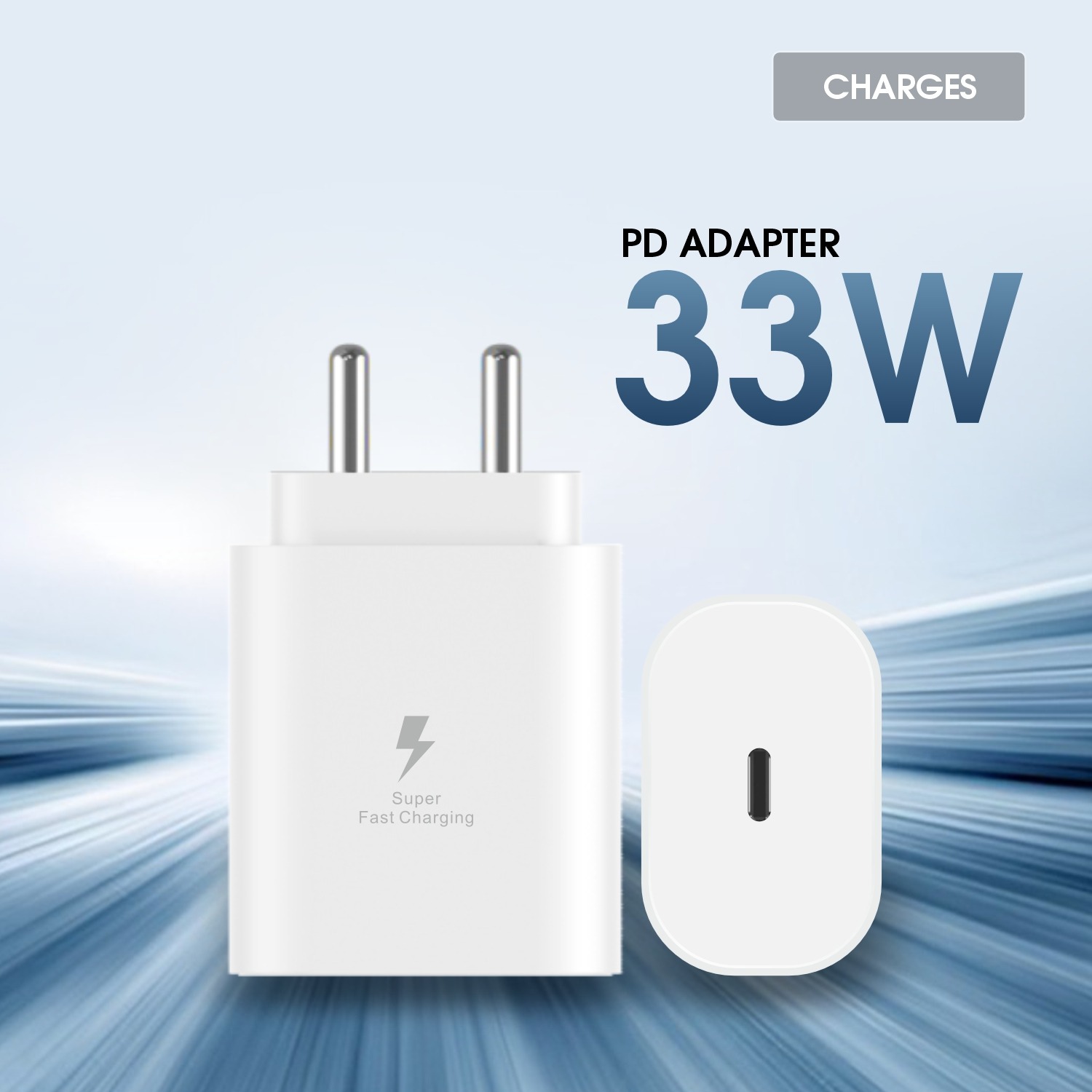
Mobile Charger
The manufacturing process of a mobile charger involves several stages, from initial design to final assembly and testing. Here’s an overview of the process:
1. Design and Development:
- Concept Design: Define the specifications, design, and features of the mobile charger, considering factors like voltage, current, size, and safety features.
- Prototyping: Create prototypes to test the design and functionality.
2. Component Sourcing:
- Electronic Components: Source key components such as transformers, rectifiers, capacitors, resistors, inductors, diodes, and integrated circuits (ICs).
- Materials: Obtain materials for the outer casing, typically plastic, ensuring it is durable and heat-resistant.
3. PCB Manufacturing:
- PCB Design: Design the printed circuit board (PCB) layout that includes the circuitry for converting AC to DC, voltage regulation, and current limiting.
- Fabrication: Manufacture the PCBs using automated machines that place and solder components onto the board using surface mount technology (SMT).
4. Assembly of Internal Components:
- Soldering: Solder electronic components onto the PCB using automated soldering machines.
- Integration: Integrate the microcontroller, voltage regulator, transformer, rectifiers, and other components onto the PCB.
- Testing: Perform initial tests on the PCB to ensure all components are functioning correctly.
5. Casing Production:
- Mold Design: Design molds for the plastic casing of the charger.
- Injection Molding: Use injection molding machines to produce the plastic casing parts.
- Finishing: Trim and finish the casing parts to ensure a smooth surface and proper fit.
6. Assembly of Charger:
- Component Assembly: Place the assembled PCB into the plastic casing.
- Wiring: Connect wires and solder connections for the AC plug and DC output.
- Encasing: Securely close the casing using screws or ultrasonic welding, ensuring all parts are firmly in place.
7. Quality Control:
- Functionality Testing: Test each charger for output voltage and current, ensuring it meets the specified ratings.
- Safety Testing: Conduct safety tests, including short-circuit protection, overcurrent protection, and temperature tests.
- Durability Testing: Perform stress tests, including drop tests and heat resistance tests, to ensure durability.
8. Certification:
- Compliance: Ensure the chargers meet international safety and quality standards, such as CE, UL, and RoHS.
- Certification: Obtain necessary certifications from regulatory bodies.
9. Packaging:
- Design Packaging: Design and produce packaging materials, including boxes, manuals, and labels.
- Packaging Assembly: Package the chargers securely for shipping, including accessories such as cables.